How GFRP Rebar Manufacturers are Contributing to Sustainable Development Goals in India
Introduction to GFRP Rebar and Sustainable Development in India
GFRP rebar, or Glass Fiber Reinforced Polymer rebar, is shaking things up in the construction world in India, and for good reason. It’s an alternative to traditional steel rebar that’s not only lighter and more robust against corrosion but also significantly more sustainable. So, what’s this got to do with sustainable development in India? Everything. As India strides towards achieving its Sustainable Development Goals (SDGs), GFRP rebar is playing a key role. These SDGs aim to address global challenges like poverty, inequality, climate change, and environmental degradation. Using GFRP rebar helps in building safer, more durable structures while also reducing carbon footprint and minimizing resource depletion. It’s a game-changer for both the construction industry and the environment. Simply put, GFRP rebar manufacturers are at the forefront of helping India build smarter, not harder, for a greener, more sustainable future
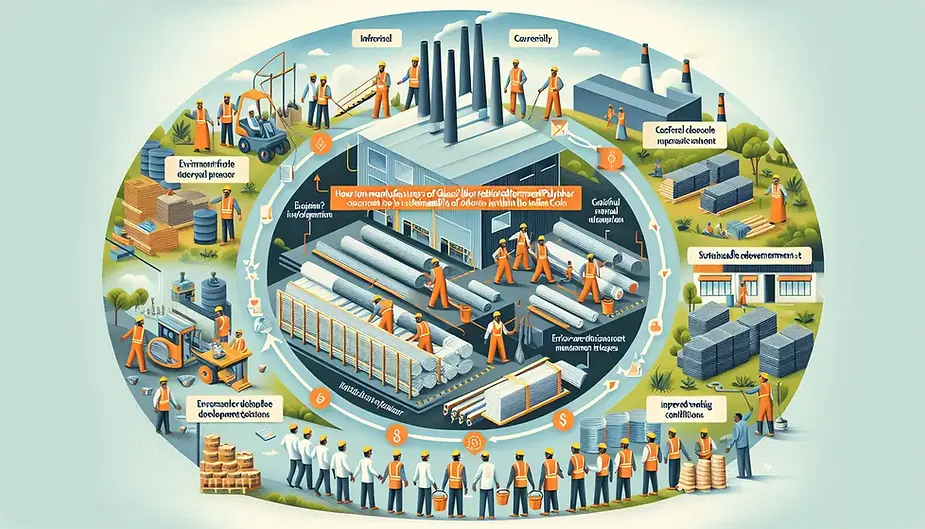
Understanding GFRP Rebar: What Makes It Sustainable?
GFRP rebar, short for Glass Fiber Reinforced Polymer rebar, marks a significant leap in construction technology, especially when talking sustainability. Here’s the straightforward scoop: traditional steel rebar, though strong, rusts over time, leading to serious structural issues and environmental concerns like increased waste and resource depletion. On the flip side, GFRP rebar doesn’t rust. This alone extends the life of structures, making maintenance a less frequent concern and reducing the overall environmental footprint. But the sustainability benefits don’t stop there.
First off, GFRP rebar is lighter than steel, meaning it takes less energy to transport and install. This directly translates to lower carbon emissions, a key goal in sustainable development. Plus, since they’re not made from metal, GFRP rebars require less energy to produce. We’re talking about a process that doesn’t involve the high temperatures and massive amounts of energy needed to forge steel, further cutting down on carbon emissions.
Then there’s the durability factor. Structures built with GFRP rebar can withstand harsh environments much better than those with steel. Saltwater, corrosive chemicals, and even alkaline environments that would speed up deterioration in steel have little to no effect on GFRP rebar. This durability means that structures don’t just last longer; they also require fewer resources for repair and maintenance over their lifespan.
By using GFRP rebar, manufacturers in India are not merely reducing the construction industry’s environmental footprint; they are actively contributing to sustainable development goals. They’re ensuring that the infrastructure being built today doesn’t just stand the test of time but does so in a way that maintains environmental integrity and pushes us towards a more sustainable future. In a nutshell, GFRP rebar is not just about building structures; it’s about building a sustainable world.
The Role of GFRP Rebar Manufacturers in India
GFRP rebar manufacturers in India are doing more than just producing another construction material. They’re playing a crucial role in pushing the country towards its sustainable development goals. You see, GFRP, or glass fiber reinforced polymer rebar, is a kind of rebar that’s not just lighter than traditional steel rebar but also doesn’t rust. This means structures made with GFRP can last longer and need less maintenance. It’s a game changer, especially in places near the sea where saltwater can eat away at steel quickly. By making buildings and infrastructure more durable, these manufacturers are helping reduce the need for frequent repairs or replacements, cutting down on the resources needed over time. Plus, GFRP rebar is made from materials that can come from recycled sources, adding another tick in the sustainability box. By bringing GFRP rebar into the mainstream construction industry, manufacturers in India are not only offering a better building solution, they’re contributing to more sustainable construction practices that are kind to the planet. It’s a big deal, showing that how we build can change the world for the better.
Impact on Sustainability Goals: A Closer Look
GFRP rebar manufacturers in India are making a real difference in reaching sustainability goals. Here’s how. First off, GFRP rebar, made from glass fiber reinforced polymer, is a game-changer because it doesn’t rust like traditional steel. This means it lasts longer, reducing the need for frequent replacements and cutting down on resource use. Plus, it’s lighter than steel, which makes transport easier and lessens fuel consumption. Big win for the environment, right? But there’s more. Using GFRP rebar also means less carbon footprint. It requires less energy to produce than steel rebar, directly supporting the goal of reducing greenhouse gas emissions. Furthermore, the durability and longevity of GFRP contribute to more sustainable construction practices. Structures built with GFRP rebar require less maintenance and repair over their lifetime. This not only saves resources but also supports the sustainability goal of promoting resilient infrastructure. All in, GFRP rebar manufacturers are not just making construction materials; they’re helping India move closer to its sustainability goals, one building at a time
Environmental Benefits of Choosing GFRP Rebar
TMT bars susceptible to corrosion. They may require replacement over time, which could increase the long-term cost of the structure. GFRP rebar, being 2 times stronger than TMT rebar implies one size lower diameter than used traditionally has a longer lifespan and requires less maintenance, making it a more cost-effective option in the long run. GFRP rebars let you save money directly as compared to the traditionally used material let alone the indirect cost savings such as 2-3% wastage of steel, transportation, on-site handling labor cost, improved labor efficiency due to low fatigue of laborer, and improved life of flooring because of their non-corrosive nature, faster construction process than with steel, etc.
Economic Advantages for India's Infrastructure
Switching from traditional steel rebar to GFRP (Glass Fiber Reinforced Polymer) rebar is a game changer for India’s economy and its infrastructure sector. First off, GFRP rebar is lighter than steel. This means it’s easier and cheaper to transport, cutting down on costs right from the start. Next, it’s corrosion-resistant. In a country with varied climates, from the humid coastlines to the cold, damp highlands, this is a big deal. Structures made with GFRP rebar last longer and need less maintenance. Less maintenance equals more savings. Then, there’s the durability factor. GFRP rebar stands up to harsh conditions without batting an eye. This leads to longer-lasting infrastructure projects, from bridges to roads, reducing the need for pricey repairs or rebuilds. By investing in GFRP, India isn’t just saving money; it’s building a more resilient future. Plus, this shift supports local industries and creates jobs, from manufacturing to construction, giving the economy a healthy boost. In short, by embracing GFRP rebar, India is setting itself up for a win-win: saving money while building infrastructure that stands the test of time.
Case Studies: Successful GFRP Implementations in India
In India, several case studies highlight how GFRP (Glass Fiber Reinforced Polymer) rebar manufacturers are revolutionizing the construction industry while supporting sustainable development. For example, the construction of the new campus of the Indian Institute of Technology in Hyderabad employed GFRP rebar extensively. This not only reduced the structure’s carbon footprint but also ensured its longevity and resistance to corrosion, especially important in India’s humid climate. Another significant project is the Kochi Metro Rail, which incorporated GFRP rebar in its construction. This choice was made to improve durability and resistance against the harsh saline environment of the coastal city, showcasing a commitment to sustainability and innovation. These case studies demonstrate the growing acceptance of GFRP rebar as a sustainable and durable alternative to traditional steel, supporting India’s goals for eco-friendly and resilient infrastructure development.
Challenges Faced by GFRP Rebar Manufacturers
GFRP rebar manufacturers in India are playing a critical role in advancing sustainable construction practices. However, they face a series of challenges that impact their operations and contributions to sustainability goals. First, the high cost of raw materials needed to produce GFRP (Glass Fiber Reinforced Polymer) rebar is a significant hurdle. These materials are often more expensive compared to those required for traditional steel rebar, which directly influences the final product’s cost.
Second, there’s the issue of familiarity and acceptance within the construction industry. Many builders and contractors are accustomed to working with steel rebar and remain skeptical about the benefits and durability of GFRP rebar despite its corrosion resistance and longer lifecycle. This reluctance can slow down adoption rates and growth opportunities for GFRP rebar in Indian construction projects.
Third, infrastructure for large-scale production and supply of GFRP rebar is still developing. Manufacturers often struggle with scaling up their operations due to limited production facilities and distribution networks. This makes it challenging to meet potential demand, particularly for large infrastructure projects across the country.
Future Directions: The Road Ahead for Sustainability and GFRP Rebar
Looking ahead, the journey towards sustainability and the role of Glass Fiber Reinforced Polymer (GFRP) rebar in it appears both promising and crucial. India, with its booming construction sector and pressing need for durable, eco-friendly materials, stands at a critical point. The future for GFRP rebar is not just about producing a material that’s stronger and lasts longer than steel without corroding, it’s about innovating responsibly.
Manufacturers are gearing up to face this challenge head-on. They are focusing on lowering the carbon footprint of production processes, enhancing the recyclability of GFRP, and ensuring that all raw materials are sourced keeping in mind ethical and environmental standards. This is important because making GFRP rebar requires less energy than steel rebar. It also doesn’t rust, which means it won’t need to be replaced as often, reducing waste.
Furthermore, research and development are in full swing to make GFRP even more effective and efficient. This includes making it stronger, more flexible, and improving its bonding with concrete, which is crucial for the safety and longevity of constructions.
Summary: GFRP Rebar's Contribution to India's Sustainable Development Goals
GFRP rebar manufacturers are changing the construction game in India, pushing the country closer to its sustainable development goals. What’s GFRP? It’s Glass Fiber Reinforced Polymer, and it’s known for being tough against corrosion, light, and having a longer life than traditional steel rebar. This makes it a game-changer for building durable, sustainable infrastructure. With India’s rapid growth, using GFRP rebar means less maintenance and repair down the line. This is not just good for the wallet but also excellent for the planet. Less steel production means a lower carbon footprint. Plus, GFRP rebar’s durability aligns with India’s aim for sustainable cities and communities. Every construction project using GFRP rebar is a step toward a more sustainable and resilient India. So, GFRP rebar manufacturers aren’t just making materials; they’re shaping a sustainable future for all.